第一节、价值流改善项目路线图
价值流改善是通过现有价值流图分析、布局分析等方面来找到不足,而后寻找改进机会,也就是爆炸点,围绕浪费、连续流、节拍等方面展开,绘制理想状态的价值流图,最后通过连续流方案的实施、布局的改变来达到理想价值流,进行优化,最终达到目标。
第二节 何时要用价值流分析?
在制造行业,价值流是将一种产品从原材料状态加工成客户可以接受的成品,并销售给用户的一整套操作过程,下面是价值流的三大范围:
A、从概念到投产的设计流程;
B、从原材料到产成品交付的生产流程;
C、从订单接受到完成订单并收到现金的订单执行流程;
企业实现精益生产管理,最基本的一条就是消灭浪费,而在企业的生产经营活动中,要消灭浪费,就必须判别企业生产中的两个基本构成:增值和非增值活动。
统计研究发现,企业生产活动中,增值活动约占企业生产和经营活动的5%。必要但非增值活动约占60%,其余35%为浪费。
价值流改善就是通过绘制价值流图,进行价值流图分析来发现并消灭浪费、降低成本,赢取最高的边际利润。
价值流图是用一些简单的符号和流线从头到尾描绘每一个工序状态、工序间的物流、信息流和价值流的状态图。
价值流图分析就是先对运作过程中的现状进行分析,即对“当前状态图”进行分析,从顾客一端开始,首先了解顾客的需求情况和节拍,然后研究运作流程中的每一道工序,从下游追溯到上游,直至供应商。分析每个工序的增值和非增值活动,包括准备、加工、库存、物料的转移方法等,记录对应的时间,了解分析物流信息传递的路径和方法,然后根据分析情况来判别和确定出浪费所在及其原因,为消灭浪费和持续改善提供目标。最后根据企业的实际情况,设计出新的价值流程,为未来的运作指明方向。
第三节、价值流改善的步骤
下图完整的讲述了价值流改善的流程,从产品族的选择开始,通过描绘现况图,规划未来图,识别改善机会,建立计划实施改善,最终实现价值流的改善。
1、产品族的选择
企业的价值流通常由客户决定。而企业可能存在很多条价值流,每种规格产品都存在一个价值流。在进行改善前,要决定需要改进的产品族。当有多个产品需要改进时,可结合产品路径分析来确定要进行改善的目标价值流。
产品族的定义:一组通过类似工序和下道相同设备的产品。
首先要按照产量从高到低的顺序,列示每种产品的作业顺序,然后将具有相同加工路线的产品结合在一起,以产品高的1~2组为目标价值流。
2、现状价值流图
现状价值流图表明“正在”发生的状态,展示了浪费的步骤和瓶颈,能帮助找到如何能够合并“流动”,也能帮助看到哪里需要“拉动”体系,揭示了生产周期。
绘制现状价值流图需要收集以下信息。
1)、识别顾客和顾客需求
了解顾客每月的需求,直至分解到每日需求。
2)、绘制整体作业流动
从原料供应商直至客户的整个作业流动过程。
3)、识别关键指标
关键指标通常包含:
作业者数量、生产速度、作业循环时间、换线时间、正常运行百分比、一次合格率、换线频率、增值时间、班次、OEE、库存、人员走动距离、产品传送距离等。
4)、物料流、生产流、信息流的收集
在本文第四节有详细介绍完整价值流图的绘制步骤。
在进行价值流改善前,识别现状价值流图上的改进点,以及实际过程中遇到的问题都可以用爆炸点来进行标识。
3、未来价值流的规划
精益生产通常有以下特点
1)、按照节拍时间生产
2)、尽可能的发展连续流
3)、无法用连续流时用超市控制生产
4)、努力使订单只下达到一个环节
5)、定节拍时,均分分配多品种产品的生产
6)、培养上游每天制造各种零件的能力
为了完成未来价值流的规划,在开始未来价值流图规划之前,需要考虑以下问题:
顾客需求 |
1、理想的操作时间(节拍时间)? 2、建立成品超市或直接发货? |
物料流 |
3、能否使用连续的流动(单件流) 4、哪里需要超市拉动系统? |
信息流 |
5、计划需要下达到哪个节点? 6、如何均衡混合生产? |
改进 |
7、所有需要改进的问题点,制定价值流改善计划 |
未来价值流图规划完成后,需要确认以下事项:
1)、未来状态是否消除了浪费的根因
2)、 新的生产周期和增值比
4、价值流改善计划
制定计划,明确做什么,谁来做,做到什么程度,什么时候完成,定期回顾价值流行动计划,确保计划可控及完成。
价值流改善计划表
目标 |
对策 |
责任人 |
完成时间 |
进度 |
备注 |
|
确定目标 |
1 |
xxxxxxxx |
xxx |
xx/xx/xxxx |
100% |
|
|
2 |
xxxxxxxx |
xxx |
xx/xx/xxxx |
75% |
|
|
3 |
xxxxxxxx |
xxx |
xx/xx/xxxx |
50% |
|
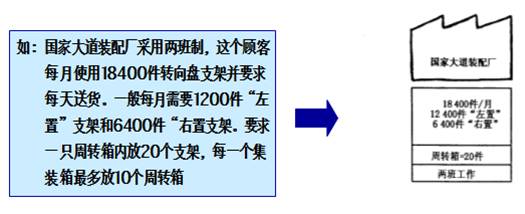
第二步:画出基本的生产过程(即生产流程步骤)
第三步:画数据箱
第四步:画出库存,标注“库存量”(同时用数量和时间标记)
第五步:画出成品运达顾客,另一头画出供应商供货情况
第六步:绘制信息流,在图的上半部从右向左画
第七步:画出时间线
那么,完整的价值流图便绘制完成了。通过价值流图的可以计算TT、CT等,并找到现状价值流图中存在的问题。
第五节、项目案例:
本项目主要通过价值流改善工具,对现有的流程进行了梳理优化,涉及的产品为某产品的不锈钢面板。通过对现场进行价值流程的分析,找到了现有价值流程中存在的浪费动作和工序,然后通过冲压、抛光、全检、打标等连线作业搭建的改进方式对工艺流程进行了重现调整,提升了生产节拍。在实施局部连续流之后,又对生产线的动作进行了详细的分析展开,调整了设备的布局,减少了搬运的浪费等。
1 项目定义
1.1 选题背景
不锈钢面板是某产品自制件最关键的零部件,随着生产产量的不断提升,品种不断增加,市场需求波动越来越大,这就需要生产能够有足够的柔性和更短的生产周期,来快速满足客户需求,因此从工厂的交付管理战略指标出发,成立面板生产周期缩短项目。
快速交付对工厂的JIT推进具有重要意义,也可以有效减少生产批量,减少库存,减少工厂场地使用面积和周转工具。
1.2 问题陈述
某产品是燃气工厂最主要的产品线,占工厂产量的90%以上(参考2014预测产量),它的自制件是燃气冲制喷涂车间负责生产的,其中关键零部件为某产品不锈钢面板、某产品底盘、某产品承液盘等三大主要零部件,底盘已经实现了机器人自动连线作业,生产周期已经大缩短,目前生产周期最长的是某产品的不锈钢面板,它将影响着整个某产品的自制件周期,所以缩短某产品面板的生产周期迫在眉睫。
1.3 项目范围
项目范围是六西格玛项目定义阶段的重要环节,对项目的实施效果和影响程度有着举足轻重的作用。本项目在项目范围确定过程中,根据项目改善对象和前后端,从SIPOC五个环节,小组成员最终确定了项目的范围。
本项目在流程方面主要涉及有冲压工艺、抛光工艺、检验工艺、激光打标工艺。项目的宏观流程图如下:
产品范围:所有A、B线生产的面板(覆盖95%以上的面板生产)
工艺范围:冲压、抛光、检验、激光打标;
涉及部门:冲压车间、喷涂车间、PMC、制造技术
1.4
Y的定义
Y--面板生产周期:即面板从仓库领料出来到面板成品做出所需要的时间为面板的生产周期。
范围:(板材领料--------面板成品入库)
面板生产周期=∑ 各工序生产及停滞时间停滞
生产周期流程示意图如下:
1.5 目标陈述
根据现状,结合六西格玛目标设置一般原则,30%以上改善作为目标,我们本次的改善目标也按照降低30%以上来设置,现状水平为5天,目标设置为3.5天,挑战目标设40%即3天。
1.6 预计收益
1、直接财务收益
① 缩短交付周期节约金额:经济效益=2500台*400元*(5-3.5)*0.056=8.4万
② 减少周转工具节约金额:(1.5天的库存量相当40辆周转车)
收益金额=40*2000元/辆=8万 合计节约金额=8.8+8=16.8万元
2、无形经济收益
① 减少场地占用面积;
② 提高生产柔性;
③ 减少搬运损耗;
④ 提高团队成员六西格玛技能;
1.7 项目组织建设
项目团队根据工作职责和利益相关方分析,确定项目的团队成员,并且对各人员进行任务分配,职责分工。为了保证项目在实施过程中顺利推进,并能够有效的获得资源的支持和提供,项目有部门总监和六西格玛推进办的黑带大师参与,为项目实施保驾护航!
1.8 项目推进计划
本项目启动时间为2013年12月26日,最终截止时间为2014年6月30日,跨度为6个月
2 测量阶段
2.1 数据来源
ERP数据财务部门每月会对现场实物核对,根据财务抽盘结果来看,每月的数据与实物数量都是一致的,可以判定系统数据真实可信。
2.2
Y的现状分析
目前面板生产工艺如下图,第一道工序为预冲孔,第二道为拉伸,同时有检验擦油工序,然后将半成品放置与拉伸半成品区域,下一步为5道冲压连线工序和抛光工序,做出来的半成品放置与待检区,接下来是清洁全检工序,完工后产品放置于带打标区域,最后是打标工序,将产品搬运至打标室进行打标,便可得冲压成品。整个工序有5处停滞。中间库存比较多,占用较多的场地和周转物流工具。
2.3 价值流现状
根据现有的生产现状得出的现状价值流图如下图,整个生产过程周期为5天时间,其中增值时间仅有258秒,其余时间都为停滞等待时间。
2.4 现状布局
车间现场布局如下,停滞节点4处,分别为预冲孔后、拉伸后、冲床连线后、清洁检验后,最终经过打标,成为冲压成品。
2.5 问题清单
通过头脑风暴最终汇总的出的几个主要问题如下表:
序号 | 问题 | 责任人 | 计划完成日期 |
1 | 生产过程停滞太多,不能连续作业,导致中间库存太多,周期较长。 | Xxx | 5月30日 |
2 | 生产节拍不统一,给连线作业造成一定困难。 | Xxx | 5月30日 |
3 | 工序过多,导致计划排产困难较多,不能够及时准确了解需求,计划体系不健全。 | Xxx | 5月30日 |
4 | 切边工序设备规格不统一,导致两条线切换柔性不够。 | Xxx | 5月30日 |
5 | 两条线的设备统一的前提是所有面板切边模具规格统一到200吨设备。 | Xxx | 5月30日 |
2.6 快赢改善
对于问题4和5,我们采用快赢的方式去解决,问题4体现出的问题是面板连线的第一台设备因为吨位较大(200T),台面较高,第一道工序要从垫仓板上取物料,因此上改道工序的节拍比后面的会慢2秒钟,节拍为12秒,导致后面会有一定的等待,该工序弯腰次数也较多,劳动强度大,所以一般在派工时尽量安排技能娴熟,体能强壮的人来做这一道工序,减少流水线的损失,因此我们通过增加升降台调节物料高度减少弯腰降低劳动强度,以缩短生产节拍。
3 分析阶段
3.1 工序能力分析
面板生产工序各个环节的单位岗位产能如下:
每工序的节拍如下:
3.2 连续流可行性分析
从上面工序的节拍分析,实现连线作业,需要将目前独立作业工序全部按照连续流的方式串接起来,前提是节拍能够匹配,工艺条件允许等。
冲床连线的前段:拉伸工序使用液压机作业,设备速度慢,要与冲床连线,必须有两台设备同时作业才能满足;如此必须开两幅拉伸模具,成本太高;同样,预冲孔和拉伸连线也是因为模具成本问题存在困难,不能克服。因此,连线不可行。
冲床连线的后段:后段工序有全检、抛光、打标,全检是纯人工作业,抛光是采用手持抛光机作业方式,打标工序可以通用到所有产品型号,因此,三道工序与前道工序连线只需要节拍的调节匹配。
3.3 连续流工艺排布
整个生产流程的岗位排布如下图,抛光2组、全检清洁2组,打标3组与前道工序采用连线作业方式。
3.4 未来价值流
未来价值流程图如下,实现了全检清洁、打标工序的连线作业,将消除了中间的两次停滞,预计可以消除停滞时间2~3天时间,总的生产周期目标为2天。
4 改进阶段
4.1 车间设备布局方案
设备的布局按照连续流的生产进行排布,将冲压后工序
抛光、清洁检验、打标按照节拍计算数量进行串联排布,实现单件流的作业方式,抛光、清洁检验按照两倍的工位进行配比,打标部分通过红外感应联动皮带链接线,确保每个打标工位都能及时拿到产品。
4.2 线体布局
新线体的布局需要将全检清洁岗位迁移至流水线后端,同时安排两位全检清洁人员来进行操作,两人完工产品汇总至后端的皮带线分别输送至每一个打标岗位。
4.3 效果确认
面板生产线连线与后工序连接生产后,直接生产出冲压成品,消除了中间的停滞情况,面板生产线连线作业生产线搭建完成,实现了冲压、抛光、全检、打标连线作业,减少了中间的周转次数,每个打标机旁的皮带线采用PLC程序控制,会及时补给到每个工位。
现在可以通过MES系统查询没到工序的报工及生产时间,从目前的数据来看,可以达到预期的2天生产周期。
5 控制阶段
5.1 作业标准化
我们对最终的生产工艺做了标准化,文件中规定了面板切边至打标工序为连线工序,排产时按照连线模式排产,取消中间停滞环节,消除中间库存。
5.2 项目改善效果
通过最新的生产计划工单统计,我们的项目最终生产周期缩短为2天。
5.3 经济效益计算
项目最终缩短交付周期为3天
1、缩短交付周期节约金额:
经济效益=2500台*400元*(5-2)*0.056=16.8万
2、减少周转工具节约金额:(3天的库存量相当80辆周转车)
收益金额=80*2000元/辆=16万
3、场地面积节约80辆*2㎡=160㎡ 场地面积节约金额=160㎡*12月*10元/月=19200元
总经济效益=16.8万+16万+1.92万=34.72万
除了经济效益之外,连续流作业实现了全检跟线,避免了批量质量事故的发生。
5.4 项目推广
面板连线应经在A线生产实践取得较好效果,接下来在B线面板线也按照连续流的模式来做,该模式也可以在冲压其他零部件进行推广,如:某产品承液盘、热水器箱体、面板等。
5.5 项目总结
通过项目成员的共同努力,最终取得了项目的成功,实现了生产周期的缩短,通过该项目我们进一步了解到连续流作业方式可以在消除搬运,中间停滞,空间节省,品质管理提升方面都有非常大的促进作用,最直接的就是缩短了产品生产周期,提高了生产排产柔性和交付响应速度。
感觉这篇文章很有内涵。
我好像见过这个项目啊, 哈哈哈
这个项目流程还行
不错的
谢谢分享